tankist
Active Member
Left the electronics alone for this evening and focused on bridges.
new removable span from the descent bridge.
the plywood is thin and flexible so i glued in a square dowel on the underside. the plastic side "panels" were to long so i cut out 4 sections from the middle and super-glued the ends. rail is not permanently attached.
DAIR #2512 approaching.
side view. it actually looks like a bridge now
while glue dried i started prototyping the culvert under the climb bridge from cardboard. no worries, there will be enough clearance when its done (some rock "blasting" will be required).
new shortened span with the plastic sides.
new removable span from the descent bridge.
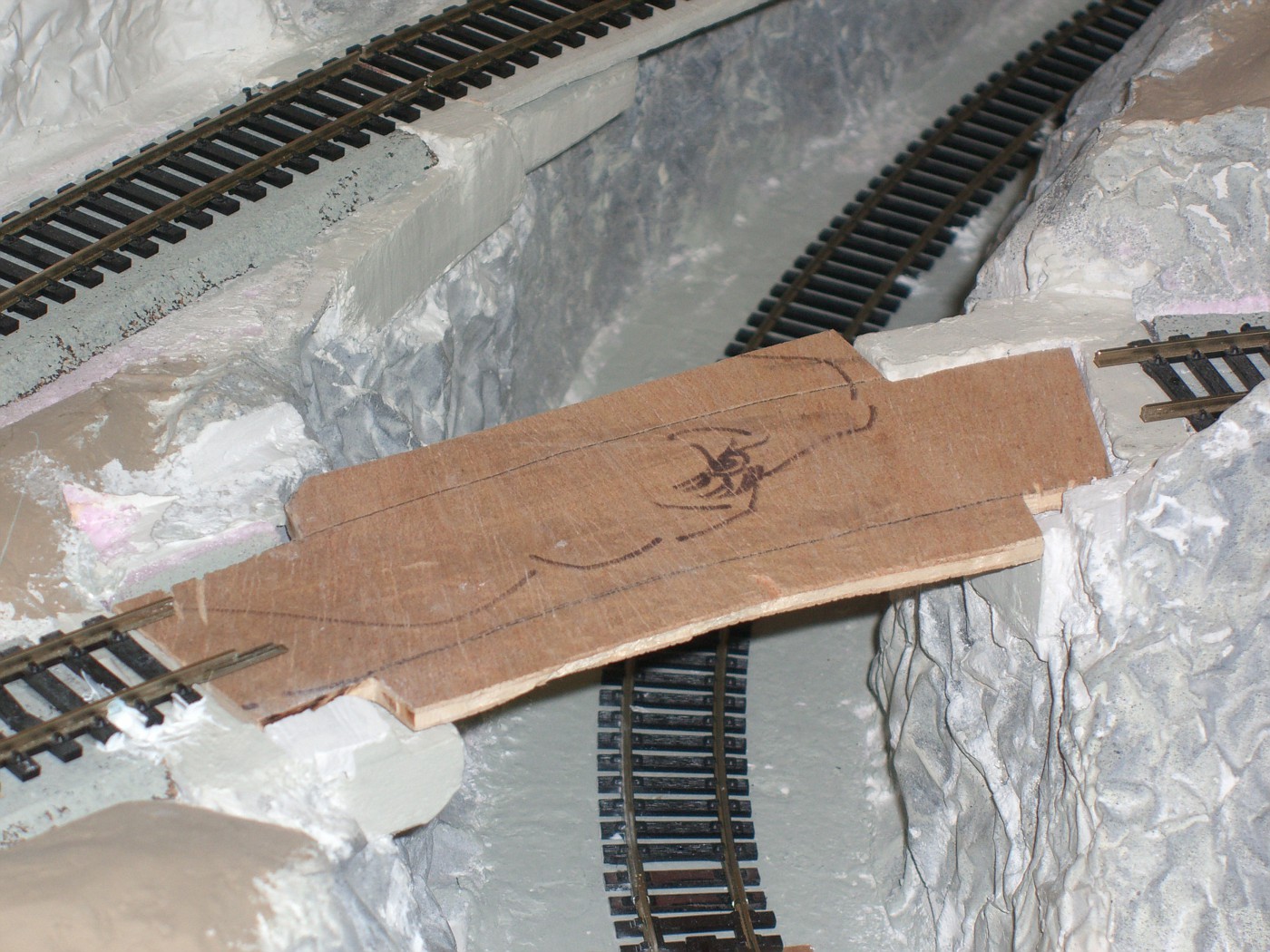
the plywood is thin and flexible so i glued in a square dowel on the underside. the plastic side "panels" were to long so i cut out 4 sections from the middle and super-glued the ends. rail is not permanently attached.
DAIR #2512 approaching.
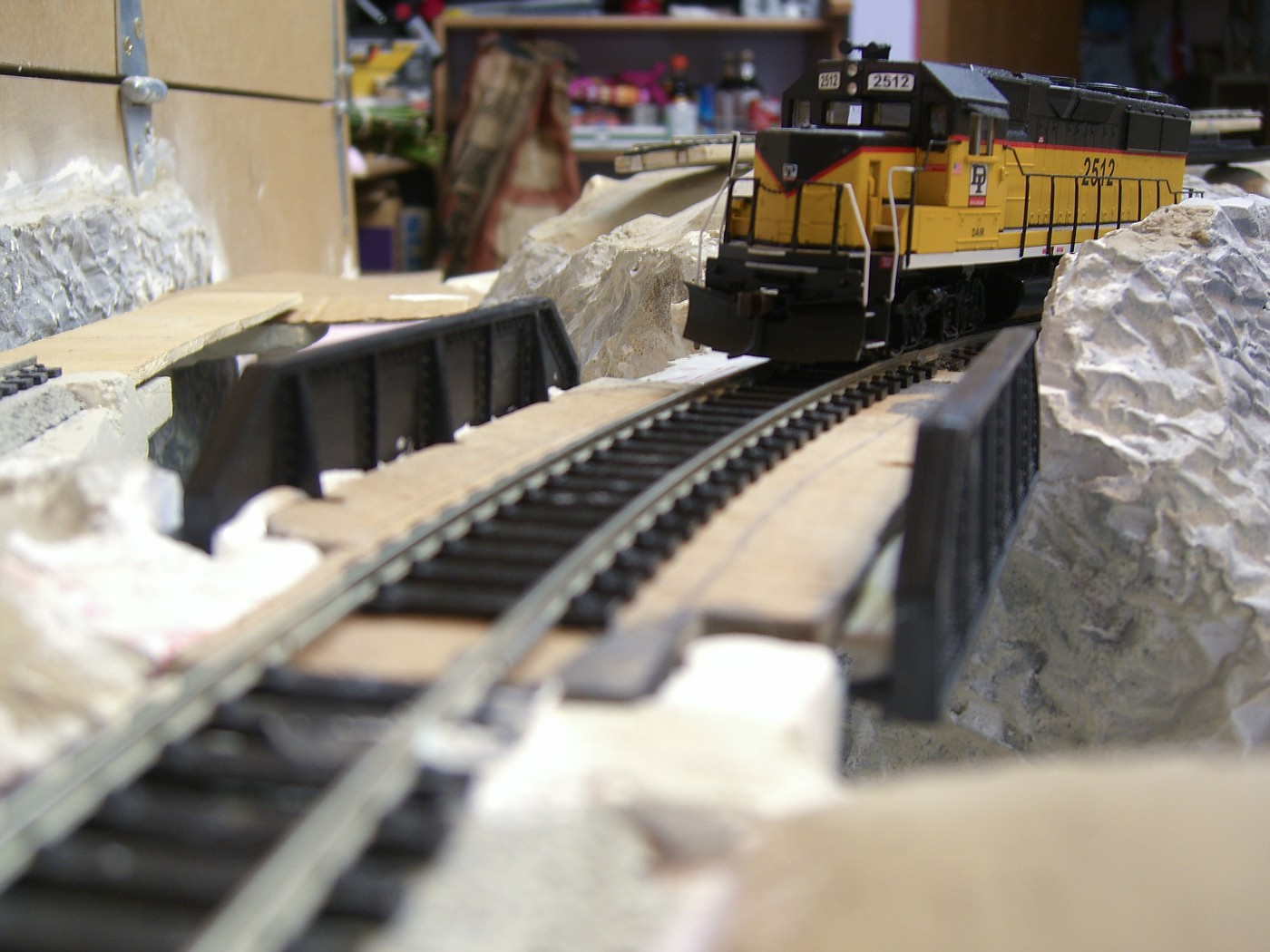
side view. it actually looks like a bridge now
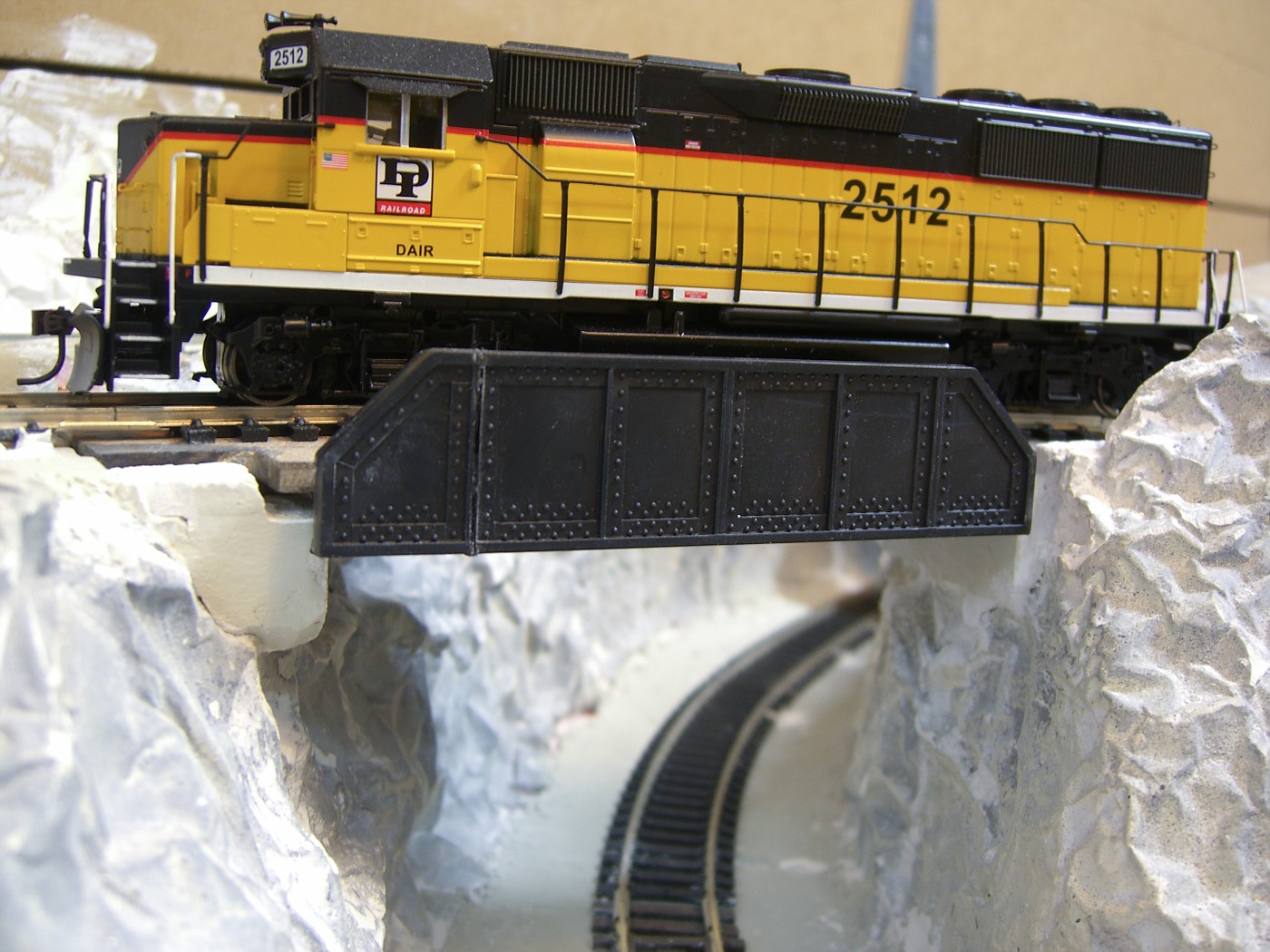
while glue dried i started prototyping the culvert under the climb bridge from cardboard. no worries, there will be enough clearance when its done (some rock "blasting" will be required).
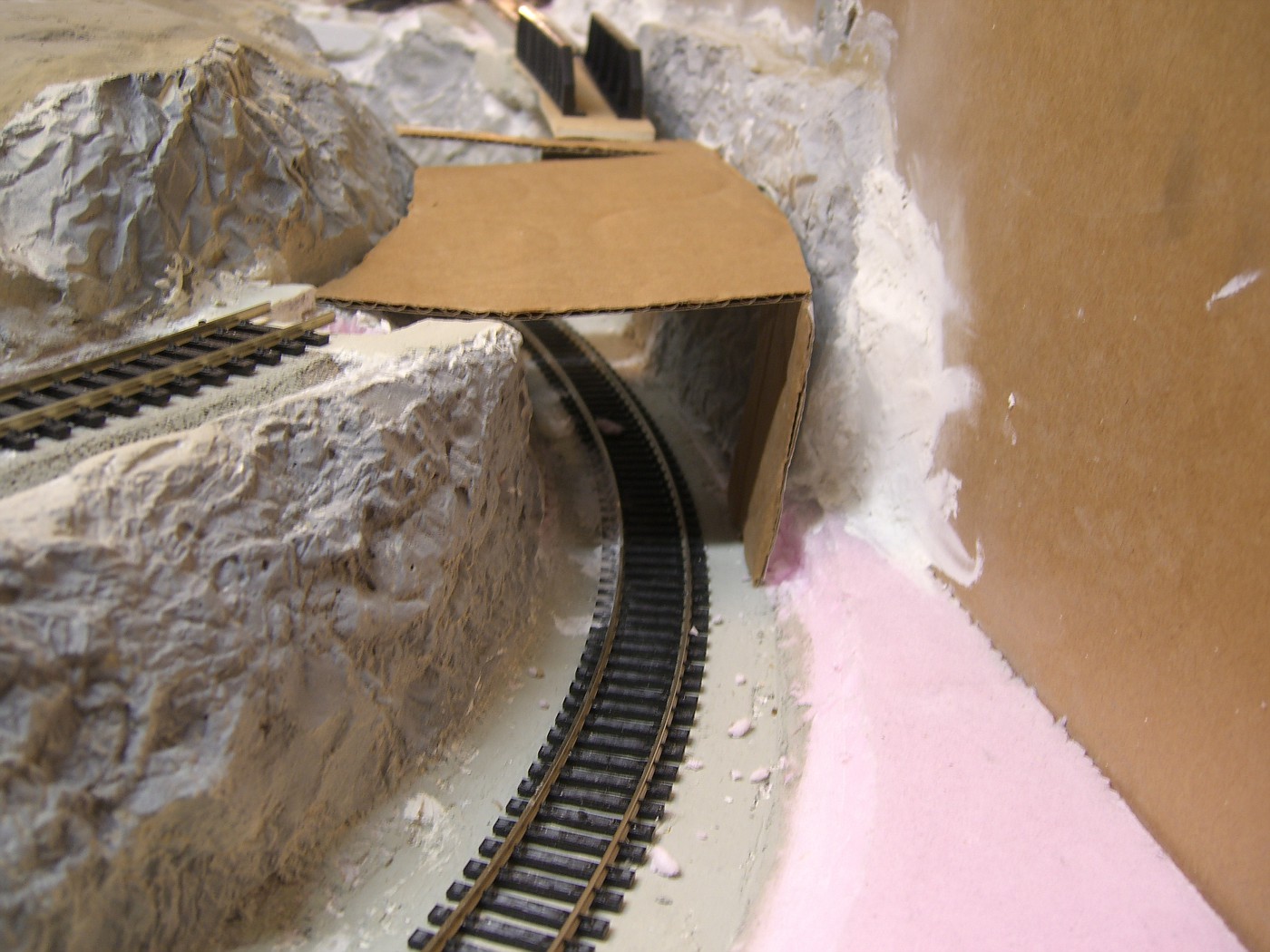
new shortened span with the plastic sides.
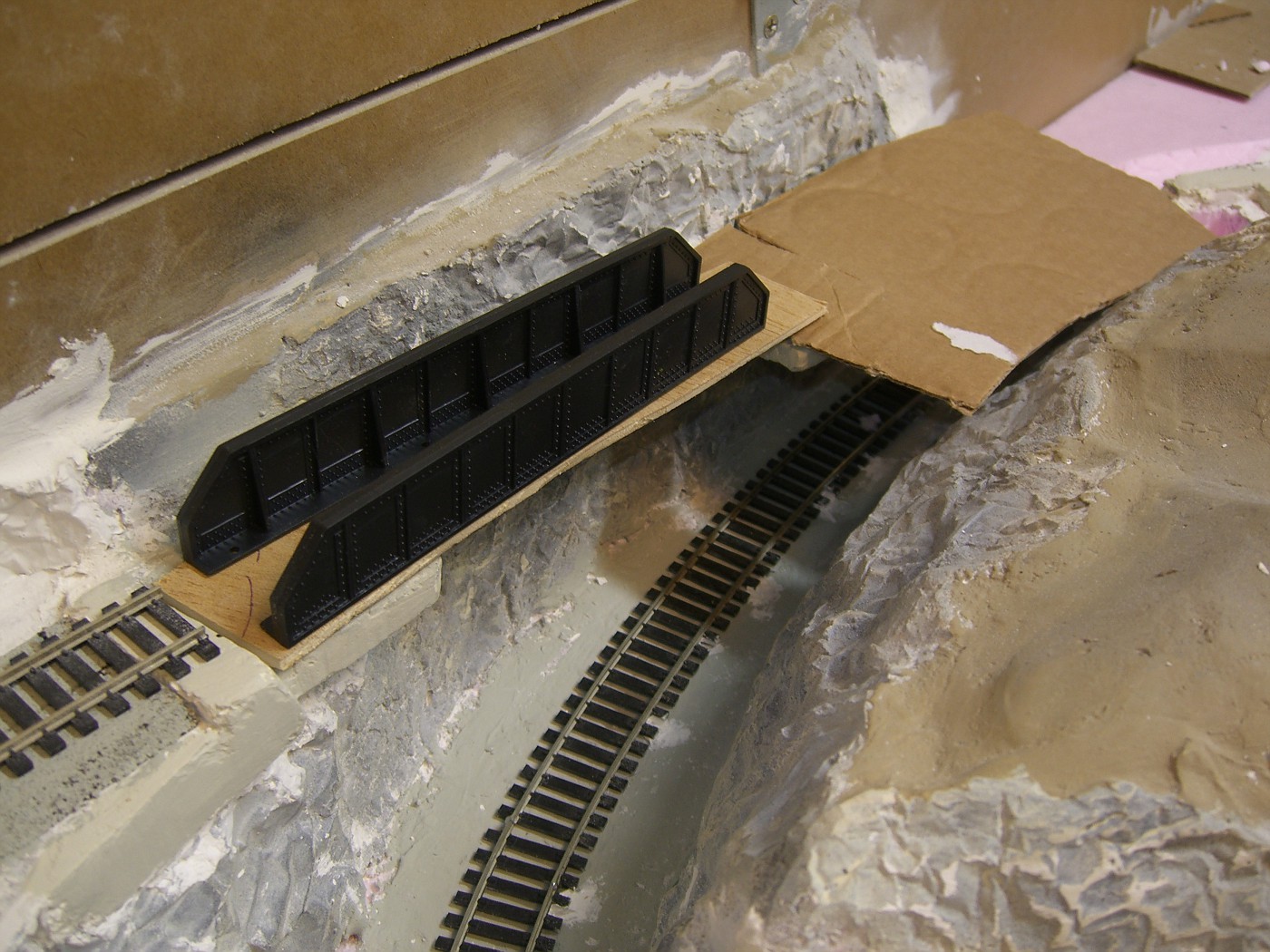
Last edited by a moderator: