IronBeltKen
Lazy Daydreamer
To some people, model railroading is an addiction; in my case, kitbashing/scratchbuilding is my “Drug of Choice.” No matter what project I may have planned, if I see an unexpected opportunity to create a home-grown model of something I’ve always wanted, I go for it! Everything else gets put on hold.
This HO scale rendition of a B&O I-5d caboose may seem totally unnecessary. After all, Spring Mills Depot announced a run of I-5’s and - if their past models are any indication - these will be very high quality and incredibly detailed. I ordered a few of them in January 2014 and who knows, they may show up any day now. But I’ve really been wanting to try scratch building one of these long before Spring Mills made their announcement. And when I noticed that the distance between the bolsters on an old worn-out brass I-12 was 19 scale feet – same as an I-5d – I realized that I might actually be able to build one using the brass I-12 chassis and some Evergreen styrene.
Since I’m modeling a line that runs near Cleveland, I wanted to model one of the many [C&O] yellow cabooses painted by a few of the shops in Ohio. I perused the rr-fallenflags.org collection of B&O rolling stock photos and found this one by Dan Dover: http://rr-fallenflags.org/bo/bo-c1979abp.jpg
C1979 had the exact same body style as the red ones I often saw in Maryland during the train-chasing days of my youth, i.e., no windows on the side with the stove. [I didn’t learn until later that all I-5d’s of this type had at least two windows on the opposite side.]
My first task was to locate some design drawings that I could scale-down to 1:87; a Google search led me to a site that had exactly what I needed. I don’t want to display those drawings here since they may be copyrighted; but I can show you the templates that I created from them:
The green-and-blue lines in the drawing represent one-inch segments that I used for sizing the image to exactly 1:87 scale.
(to be continued...)
This HO scale rendition of a B&O I-5d caboose may seem totally unnecessary. After all, Spring Mills Depot announced a run of I-5’s and - if their past models are any indication - these will be very high quality and incredibly detailed. I ordered a few of them in January 2014 and who knows, they may show up any day now. But I’ve really been wanting to try scratch building one of these long before Spring Mills made their announcement. And when I noticed that the distance between the bolsters on an old worn-out brass I-12 was 19 scale feet – same as an I-5d – I realized that I might actually be able to build one using the brass I-12 chassis and some Evergreen styrene.
Since I’m modeling a line that runs near Cleveland, I wanted to model one of the many [C&O] yellow cabooses painted by a few of the shops in Ohio. I perused the rr-fallenflags.org collection of B&O rolling stock photos and found this one by Dan Dover: http://rr-fallenflags.org/bo/bo-c1979abp.jpg
C1979 had the exact same body style as the red ones I often saw in Maryland during the train-chasing days of my youth, i.e., no windows on the side with the stove. [I didn’t learn until later that all I-5d’s of this type had at least two windows on the opposite side.]
My first task was to locate some design drawings that I could scale-down to 1:87; a Google search led me to a site that had exactly what I needed. I don’t want to display those drawings here since they may be copyrighted; but I can show you the templates that I created from them:
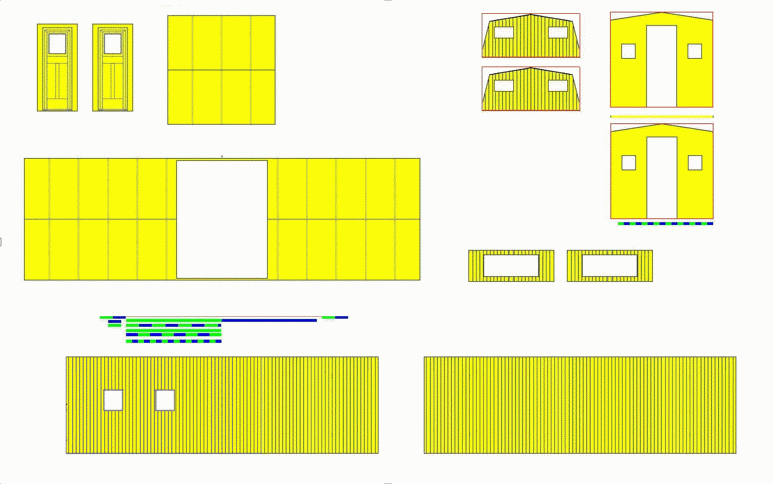
The green-and-blue lines in the drawing represent one-inch segments that I used for sizing the image to exactly 1:87 scale.
(to be continued...)